|
3.2.1.1IE(Industry Engineering 経営工学) |
|
要件項目 |
要件項目内容 |
|
1)IEによる
要件対応
2)IEとは
@IEの定義
AIEの目的
3)IEによる
標準化
|
1)IE(Industry Engineering 経営工学)による要件対応 |
・コミュニケーション面:工程・作業標準化 |
製品面:製品・工程の標準化 |
ヤル気面:製造標準化と改善力向上 |
2)IE(Industry Engineering 経営工学)とは |
@IEの定義 |
・IE(Industry Engineering 経営工学)とは、人、材料、設備を総合 |
したシステムの設計、改善、確立に関する活動で、そのシステム |
から得られる結果を明示し、予測し、評価するために、工学的 |
分析、設計原理、方法、手法と共に数学(統計)、物理学、社会 |
科学の専門知識と経験をよりどころに行う。 |
|
A数式によるIEの目的 |
Output(出来高) UP |
生産性=――――――――――――― |
Input(投入工数) DOWN |
・あらゆる産業において、下辺の工程、作業等の投入工数を最少に、 |
上辺を最大にし、生産性を向上する活動 |
3)IE(Industry Engineering 経営工学)による標準化 |
・作業測定による現状作業の標準化 |
・方法工学による改善作業標準化 |
・作業測定による世界標準時間によるヤル気の測定 |
|
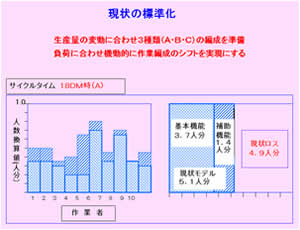
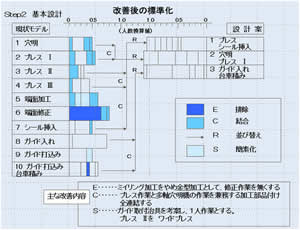
|
4)IEによる
標準化の方法
4)-1コミュニケーション
a通常チャンネル |
|
4)IE(Industry Engineering 経営工学)による標準化の方法 |
4)-1コミュニケーション 工程・手順の標準化 |
a通常チャンネル |
・工程・作業順標準化 |
@方法の標準化:手作業、工具仕様、機械化作業等方法を決める |
A手順の標準化:人により異なる、段取り作業、本作業の手順を決める |
B回数の標準化:ロット、都度、1個繰り返し等、作業回数を決める |
C時間の標準化:平均値、最速値、1/4選択値、標準時間の時間設定 |
・時間標準は、現状値時間標準と、改善後値時間標準がある |
・時間標準は用途に応じ、作業レベルを考慮して要設定
|
・プロセス・作業のレベル |
IEの定義で示した、『人、材料、設備を総合したシステム』は、下記の |
ワークシステムレベルで示され、プロセス・作業のレベルを意味する。 |
レベル |
ワークシステムレベル |
説明 |
10 |
社会環境システム |
通信、エネ、環境、交易、行政デジタル社会 |
9 |
利害関係者 |
事業関連団体 |
8 |
Office,Factry(事業所工場) |
製品群事業単位、サプライチエーン |
7 |
Sction(課) |
製品加工組立の管理単位 |
6 |
Function (機能・係) |
類似部品複数ライン |
5 |
Activity(単位業務) |
加工工程、組立工程のライン形成 |
4 |
Process(工程、工程系列) |
穴明、溶接等の加工工程系列 |
3 |
Operation(単位作業) |
溶接等の工程を構成する作業 |
2 |
Element(要素作業) |
SW測定できるシーケンス動作 |
1 |
Motion(動作) |
規程時間測定できる作業の最小単位 |
|
 |
bリスクチャンネル |
bリスクチャンネル |
・時間増ネック不特定 |
・作業のレベルを理解し、適した測定をしないと、手順の標準化が不十分 |
で、体系化、整合化された工程・作業の標準化とはならない。 |
・作業者の属性が変わると、作業時間は変わる。前記の方法、手順、回 |
数、時間の標準化をすることで、1つの標準時間を決める事ができる。 |
・測定法は、次に示す、作業のレベルごとに適した測定法がある |
PTS (規程時間法):動作、要素作業レベルの標準時間設定法 |
・SW(ストップウォッチ法):要素作業、単位作業をSWで測定し時間設定 |
ラインバランス:工程系列の中で、単位作業を山積み、山崩し |
リードタイム:生産計画のサイクルの中で、納期設定 |
生産サイクル:生産計画の中でサプライチェーンの計画サイクル |
|
|
cチャンスチャンネル |
cチャンスチャンネル |
・階段目標 |
より上級の時間標準にて改革管理を可能にする |
@世界通用企業標準時間:PTS(MTM、WF等) |
A他社連携(下請け階層)時間標準::SW時間 |
B納期時間:時間標準はな経験で期間指示 |
PTS:Predetermined Time Standard-既定時間標準法- |
MTM:Methods Time Measurement-標準時間設定法- |
WF:Work Factor-標準時間設定法- |
SW:Stop Watch-ストップウォッチ時間設定法- |
|
|